KOHLER
Integrated Warehouse
Project Introduction
KOHLER, a global leader in kitchen and bath products known for innovation and quality, faced growing pressure to modernize its warehouse operations amid rapid business expansion. To keep pace with increasing SKU complexity and order volume, KOHLER partnered with Hai Robotics to upgrade its fulfillment capabilities with advanced automation.
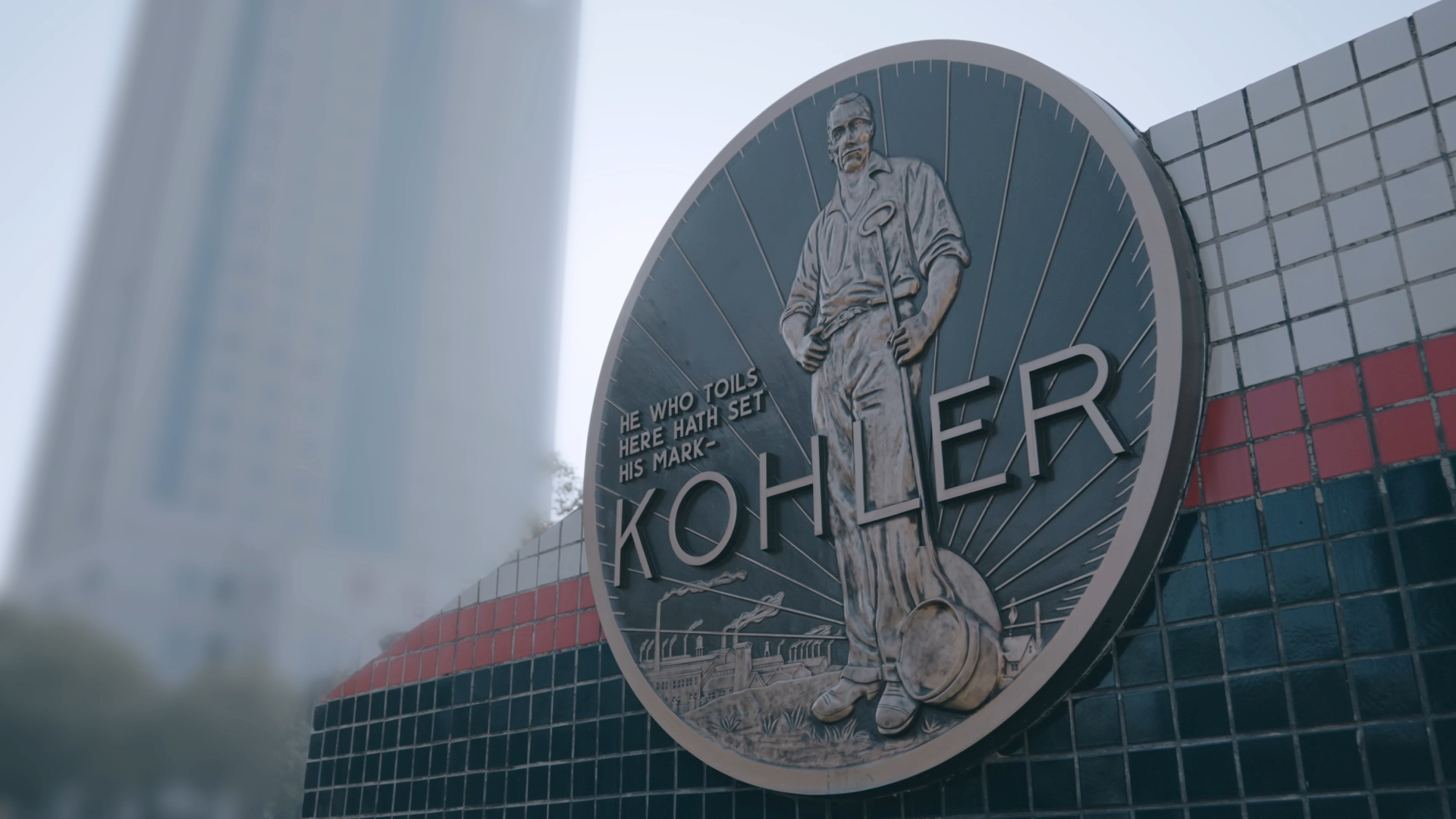
The Challenges
Before automation, KOHLER’s warehouse encountered several critical issues:
-
SKU Complexity: Managing a broad and diverse product range with varying sizes and storage needs.
-
Space Constraints: Limited warehouse footprint restricted storage capacity and slowed picking throughput.
-
Labor-Intensive Processes: Manual picking and replenishment led to slow order cycles, high labor costs, and frequent errors.
-
Scalability Limits: Traditional storage lacked flexibility to adapt to fluctuating demand and future growth.
To support its rapid growth and complex inventory needs, KOHLER partnered with Hai Robotics to deploy the HaiPick System 3 — an Automated Storage and Retrieval System (ASRS) designed to automate storage and order fulfillment in warehouses. This project aimed to transform KOHLER’s warehouse into a highly efficient and scalable operation. Key system specifications include:
Automation Area: 1,100 square meters
Shelving Height: 7.8 meters
Robots: 4 Autonomous Case-handling Mobile Robots (ACRs) + 10 Fast-Transit Companion Autonomous Mobile Robots (AMRs)
Workstations: On-robot picking workstations
Storage Capacity: Double-deep storage, accommodating 28,000+ storage locations
Outbound Efficiency: 110+ totes/hour
Since deploying the HaiPick System 3, KOHLER has realized:
-
3.7x Storage Capacity: By implementing 7.8-meter double-deep and bridge racks, KOHLER's storage capacity has expanded from 20,000+ to over 110,000 SKUs without increasing the warehouse footprint, maximizing space utilization.
-
2x Throughput Efficiency: Achieved 110+ outbound totes per hour, effectively doubling warehouse operational efficiency.
-
80% Reduction in Labor Costs: Replaced manual handling of heavy totes with automated storage and retrieval and ergonomic picking workstations, boosting productivity and reducing labor intensity by 80%, allowing staff to focus on higher-value tasks.
-
Enhanced Operational Visibility: Real-time system status and integration with SAP empowered proactive decision-making and refined inventory control.
-
Future-Proof Flexibility: Easy-to-install and scalable system design supports KOHLER’s ongoing growth and evolving business needs.