LENOVO
Production Facility
Customer Overview
Lenovo, a global tech leader renowned for its innovative laptops, smartphones, and smart devices, operates a high-output production facility in China, where a new smartphone or tablet rolls off the line every 0.6 seconds, generating over $50 billion annually. Having successfully deployed HaiPick System 1 in 2021 and 2022, Lenovo chose to deepen its partnership with Hai Robotics to keep pace with its rapid growth and push the boundaries of smart manufacturing and supply chain innovation.
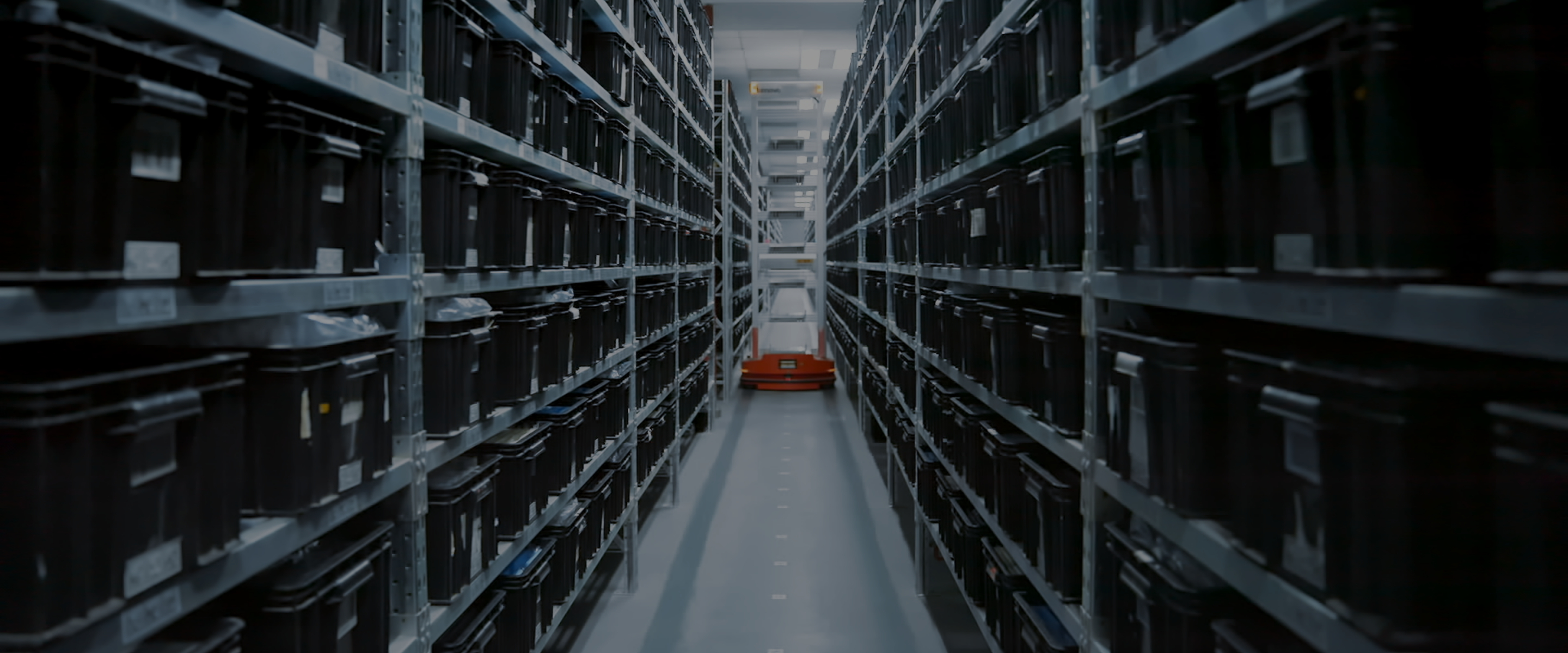
Before automation, Lenovo’s warehouse faced several critical challenges:
-
Limited Space: Storage density and material flow were restricted by the facility’s footprint.
-
High Throughput Demands: Daily production volumes of 240,000 LDA units required faster, more reliable material handling.
-
Strict Quality Control: Maintaining over 99% accuracy in material preparation and full traceability was essential to ensure zero-defect manufacturing.
-
Sustainability Goals: The need to reduce energy consumption and carbon footprint aligns with Lenovo’s commitment to green manufacturing.
-
Scalability & Flexibility: The system had to adapt dynamically to fluctuating production volumes and diverse product mixes.
To keep up with rising demand and increasing operational complexity, Lenovo partnered with Hai Robotics to deploy the HaiPick System 3 at its facility. This implementation establishes a highly efficient and flexible supply chain foundation that seamlessly supports Lenovo’s manufacturing process, from raw materials all the way through to finished products. Key system specifications include:
Automation Area: 1,100 square meters
Shelving Height: 3.2 meters
Robots: 8 Autonomous Case-handling Mobile Robots (ACRs) + 18 Fast-Transit Companion Autonomous Mobile Robots (AMRs)
Workstations: 1 inbound workstation, 1 buffer workstation, and 1 outbound workstation
Storage Capacity: Double-deep storage, accommodating 12,000+ storage locations
Outbound Efficiency: 320+ totes/hour
The deployment of the HaiPick System 3 delivered a compact yet powerful automation solution that transformed warehouse operations and unlocked significant business benefits:
-
40% Boost in Storage Density: Lenovo expanded storage capacity to hold over 12,000 totes and 650,000 LDA components, increasing storage density without expanding the footprint.
-
5-6x Faster Operations: ACRs and AMRs work in harmony, achieving throughput of 320 totes per hour and supporting daily output of 240,000 LDA parts, meeting peak production needs.
-
Dynamic Storage & Fast Access: The system automatically segments inventory into “hot” and “cold” zones based on turnover, placing high-turnover items closer to picking stations to accelerate order fulfillment.
-
Sustainable Operation: Fully automated “lights-out” workflows reduce labor costs by enabling unmanned 24/7 operation while cutting energy consumption and carbon footprint, aligning with Lenovo’s green manufacturing goals.
-
Near-Perfect Accuracy: Strict quality controls maintain over 99% accuracy in material handling, ensuring zero-defect supply chain performance.